What is manufacturing?
Manufacturing is the process by which raw materials and parts are converted into finished products. These products are then sold to wholesalers or retailers, who then sell them to the end consumer. Manufacturing as an industry makes up roughly 15% of the US’s economic output.
In recent years, manufacturing has become a business. Today, whole companies exist with the sole purpose of creating or building products for other businesses. Utilizing factories of robotic machines, computer technology, and human workers, they can assemble finished goods from any number of raw materials.
Often, manufacturers are confused with wholesalers, but these are two completely different. Any company can procure finished goods from either a wholesaler or a manufacturer. What’s different between them is that the manufacturer produces the goods themselves.
Conversely, a wholesaler buys the products from the manufacturer to sell them to other retailers. They do not make the products. They act as middlemen in the process, acquiring goods for retailers and sellers.
The different kinds of manufacturing production
Manufacturing businesses do not all make their products the same way. Depending on the buyer’s requirements, there are three different types of production:
- MTS – Make to stock
- MTO – Make to order
- MTD – Make to assemble
These three types are determined by the needs of their customers and have their pros and cons.
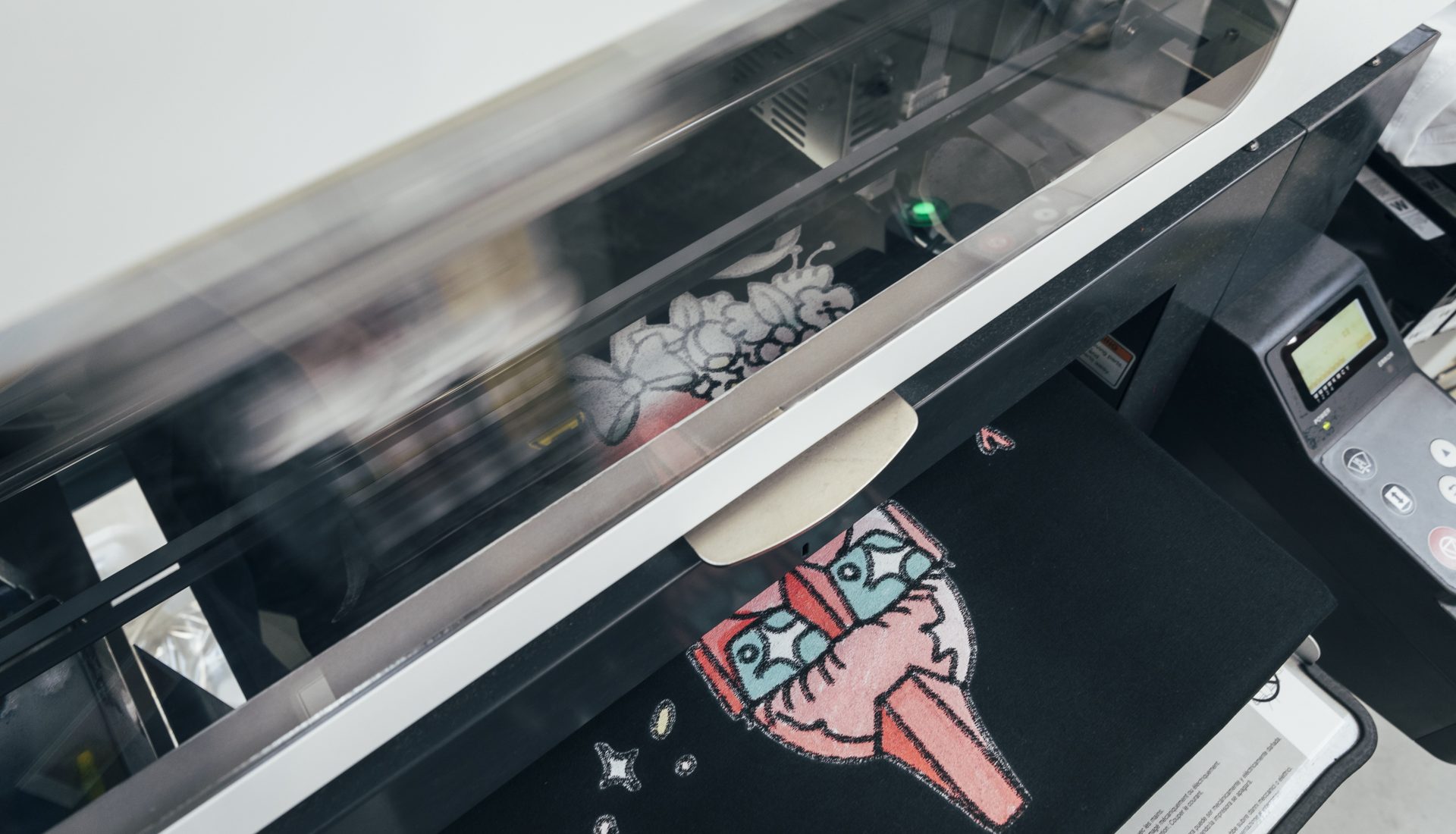
Make to stock (MTS)
This is the most simple of all production plans. It works because a set number of finished goods will be required to be kept on hand for sale. The manufacturing company will plan this number according to previous sales records. For example, if the average month sees 1,000 chairs being sold, they will continue to make 1,000 more each month. The problem with this style of manufacturing is that it doesn’t take fluctuations of sales into account. If one month should see a drastic drop in sales, this can lead to an excess in stock. If there is a boost in sales, the company may not have the necessary stock to meet demand.
Make to order (MTO)
This plan consists of buyers making orders for products that fit item amount and style specifications. This allows the manufacturer to know precisely what will be made for each order and only produce that many finished goods. However, this means longer production times. Since each item will need to be planned for after the order, the buyer can’t walk away with their purchase. Production takes time and runs the risk of being disrupted by material procurement issues but will not result in excess stock.
Make to assemble (MTA)
This plan is a midway point between the two previous ones. Working on a prediction of demand based on previous sales, the production company keeps stocks of the necessary parts on hand. As each order comes in, the raw materials can be assembled into the required products quickly. This allows for a greater degree of customizability for the customer while also cutting production times. However, this does come with the drawback of the potential for excess material stock if orders should drop.
Regardless of production strategy, each style has its risks and rewards. Losses can be made through stock buildup or lack of sales, while overproduction will cost more with less return. A fine balance between low production costs and good business foresight must be maintained to keep things running smoothly and profitably.